Overview of the application of magnesium alloys in automobiles
Volkswagen AG was the first automobile company to apply magnesium alloy on a large scale in automobiles. As early as the 1930s, Volkswagen began to use magnesium alloys. Especially since the 1990s, Germany has been a world leader in the field of magnesium alloys; Mercedes-Benz Automotive first applied magnesium alloy pressure castings to car seat brackets, and Audi Motors Inc. first introduced magnesium alloy pressure casting instrument panels. In recent years, the gearbox housings of Passat, Audi A4 and Audi A6 have used AZ91D magnesium alloy, which is 25% lighter than aluminum alloy parts.
In the United States between 1948 and 1962, millions of magnesium alloy castings were produced by pressure casting for use in automobiles. For the past ten years, automotive companies such as Ford, GM and Chrysler have been working on magnesium alloy automotive castings such as steering column frames, clutch housings, intake manifolds, clutch plates, cylinder heads, mounts, and oil filter housings. The development and application of the same, the substitution effect is obvious, greatly promoting the development of magnesium alloy.
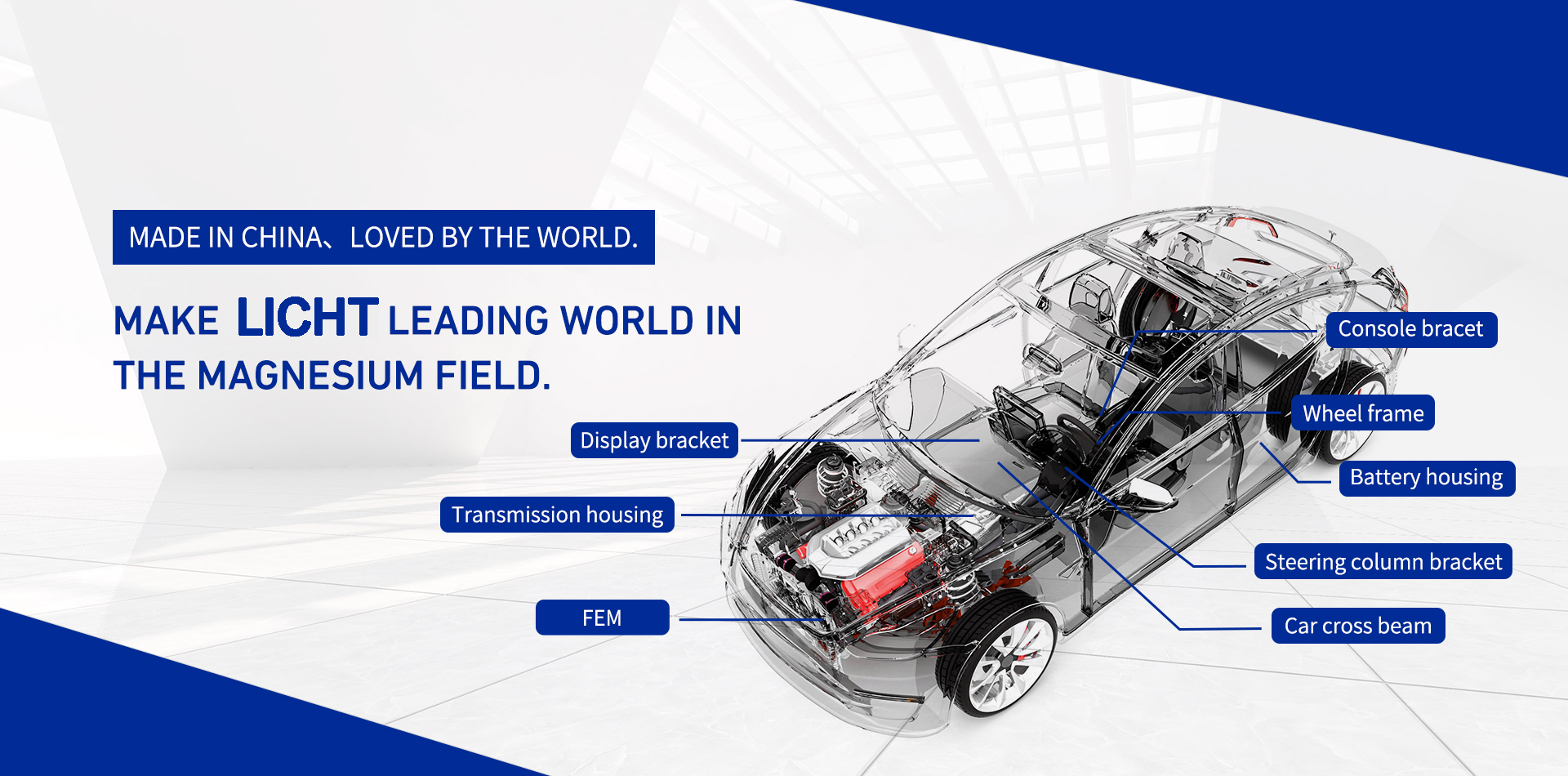
Japan has developed a low-pressure casting machine for magnesium alloys. As a result, a series of magnesium alloy pressure casting products have been developed through research. For example, Toyota Motor Corporation first manufactures magnesium alloy automobile wheels, steering shaft systems, cam covers and other components. Various automobile companies in Japan produce and apply a large number of pressure castings of magnesium alloy casings.
In China, casting magnesium alloy has been used for more than 30 years, but it was mainly used in the aerospace industry's shell, wheel and base. It started late in the automotive industry. At present, only nearly 100 companies are engaged in magnesium alloy pressure casting. Production and research. SAIC, FAW, Dongfeng Motor Corporation and Changan Automobile have played an important role in the research and development of magnesium alloys in the automotive field. In the early 1990s, SAIC first applied magnesium alloys to automobiles in China, and for the first time used magnesium alloy transmission covers, housings and clutch housings on Santana cars. At present, the production and application technology of its magnesium alloy automotive transmission housing is very mature. The magnesium alloy motor housing castings are being tested on electric vehicles. FAW has developed a high-performance magnesium alloy that can be used to manufacture automotive powertrain components under high-temperature load conditions. It has also successfully developed magnesium alloy pressures such as foot pedals, cylinder covers, supercharger housings, steering wheels, and transmission case covers. Casting parts have been used in production. Dongfeng Motor Corporation has developed a complete set of technologies for the production of auto parts in the magnesium alloy cold chamber pressure casting process in combination with the current status of China's auto parts pressure casting production equipment. With the support of the National Science and Technology Support Program, Changan Automobile completed the design, analysis, mold development and production of prototypes of large-scale complex magnesium alloy pressure castings represented by magnesium alloy transmission housings, oil pans and cylinder head covers. Successfully developed the first domestic magnesium alloy seat and loaded the vehicle and passed the regulatory test verification, and combined with Chongqing University to develop the extrusion force casting magnesium alloy automobile wheel hub.